From Lab to Scale: A Game-Changing Approach to Peptide Purification in GLP-1 Manufacturing
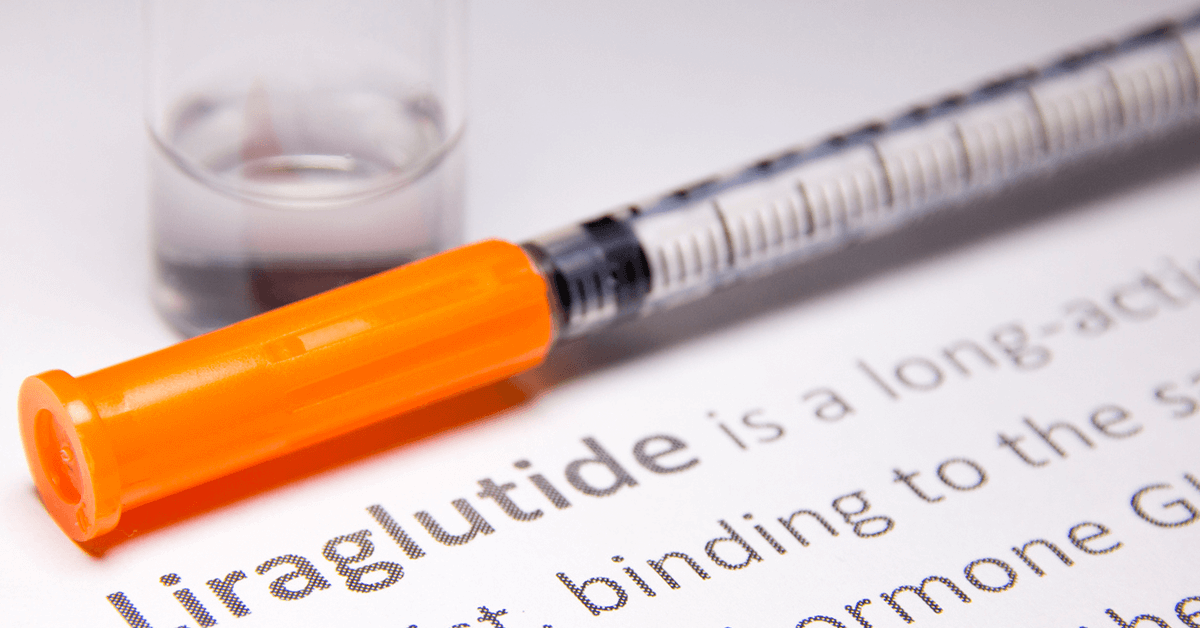
In the rapidly evolving landscape of peptide therapeutics, particularly with the surge in GLP-1 receptor agonists, manufacturing efficiency has become a critical differentiator. A study published in Chimica Oggi - Chemistry Today by Berger et al. presents a compelling case for rethinking traditional purification approaches in peptide manufacturing, using liraglutide as a case study.
From https://pdb101.rcsb.org/global-health/diabetes-mellitus/drugs/incretins/drug/liraglutide/liraglutide
The Business Challenge
According to an article published by Fierce Pharma, GLP-1 receptor agonists will generating close to $50 billion in annual sales in 2014. Manufacturers are facing increasing pressure to develop efficient, cost-effective production methods to meet the surging demand. However, traditional chromatographic purification, while effective, presents significant challenges at scale:
- High solvent consumption affecting operational costs
- Limited scalability impacting production capacity
- Complex handling of modified peptides affecting throughput
- Substantial infrastructure requirements driving capital expenses
A Novel Solution
The study introduces an innovative orthogonal purification technology called PurePep® Easy Clean (PEC), demonstrating its application in liraglutide production. This catch-and-release methodology offers several strategic advantages by providing an orthogonal approach to traditional chromatography.
Operational Efficiency: The study demonstrates the successful implementation of PEC technology for liraglutide purification, showing that the method can effectively handle complex, modified peptides while maintaining product quality.
Scale-Up Success: The researchers demonstrated seamless scalability from initial testing through gram-scale production. Importantly, the study showed consistent results across scales, maintaining product quality while increasing batch sizes.
Cost Implications
The paper presents a compelling economic analysis of PEC implementation in manufacturing scenarios:
Material Costs:
- Comparable single-use material costs to traditional methods at multi-kg scale
- Potential for significant solvent reduction
- Lower infrastructure requirements for handling and storage
Productivity Metrics: The study suggests that a manufacturer using PEC technology could process approximately 5 mol (roughly 6 kg) of pre-purified liraglutide in a single run per day, using about 1,500 L of solvent per kg of purified peptide. For comparison, traditional HPLC systems with 60 cm diameter columns typically require about 5,000 L of solvent per kg to achieve similar results. |
Strategic Implications
For organizations entering or expanding in the peptide therapeutics space, this research highlights several key benefits when exploring innovative purification technologies like catch-and-release:
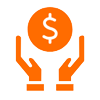
Infrastructure Investment
- Lower capital expenditure requirements
- Reduced facility space needs
- Simplified scaling pathway
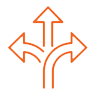
Operational Flexibility
- Easier handling of complex peptides
- Adaptable to various manufacturing scales
- Reduced dependency on specialized equipment
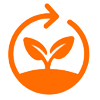
Sustainability Benefits
- Potential for reduced solvent usage
- Lower environmental impact
- Improved workplace safety profile
Looking Forward
As the peptide therapeutics market continues to grow, particularly in the GLP-1 space, manufacturing efficiency will increasingly determine market success. The study suggests that orthogonal purification technologies like PEC could provide a significant competitive advantage, particularly for organizations looking to enter or expand in this space.
For decision-makers evaluating peptide manufacturing strategies, this research provides valuable insights into potential approaches that could significantly impact both operational efficiency and bottom-line results. The demonstrated success with liraglutide, a commercially significant peptide therapeutic, makes this particularly relevant for organizations considering their manufacturing strategy in the growing GLP-1 market.
The study represents a significant step forward in peptide manufacturing technology, offering a pathway to more efficient, cost-effective production methods that could help meet the growing demand for peptide therapeutics while maintaining quality and reducing operational complexity.
Reference:
Berger et al. 2021, Chimica Oggi – Chemistry Today, 39, 38-41